Expert Installation and Unmatched Operational Support
Ensure peak performance and reliability with our comprehensive installation and operational support services. From setup to maintenance, we’ve got you covered every step of the way.
Professional Installation & Training Services
Ensure seamless integration and optimal performance with our expert installation services. Our team of experienced technicians will handle everything from site assessment and system set-up to in-depth training for advanced operation. With meticulous attention to detail and a commitment to excellence, we guarantee a smooth start for your cryogenic equipment. Trust us to set the foundation for reliable and efficient operations.

Comprehensive Site Assessment
A thorough evaluation of your facility to ensure optimal equipment placement and integration.

Professional Installation
Expert assembly and setup of your cryogenic equipment for seamless and efficient operation.

Advanced Training
In-depth training sessions to equip your team with the skills needed for advanced system operation and maintenance.
Dependability You Can Trust
At IMTEK Cryogenics, we specialize in the production and application of cryogens—substances used to achieve extremely low temperatures. Our advanced cryogenic solutions play a crucial role in a variety of industries, from medical and scientific research to space exploration and energy storage. Discover how our cutting-edge cryogenic technology is transforming the way we understand and utilize the power of cold.
Maintenance Programs
- First maintenance at 8,000 hours (approximately two years), made simple and cost-effective with our user-friendly GM technology.
- Scheduled and preventive maintenance to minimize downtime and extend equipment life, keeping costs low.
Emergency & Technical Support
- 24/7 emergency response for critical issues.
- Direct access to experienced technicians via phone, email, or live chat.
- Remote diagnostics and troubleshooting.
Performance Monitoring
- Regular assessments and optimization recommendations.
Parts and Repairs
- Genuine parts available for repairs and replacements.
- Quick turnaround times for all repairs.
User Manuals & Installation Guides
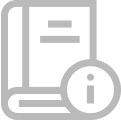
Detailed user manuals for operation and maintenance
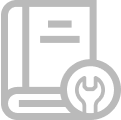
Step-by-step installation guides
Troubleshooting Tips for Cryogenic Systems
Check Power Supply:
- Ensure the system is properly connected to the power source with no electrical issues.
- Verify the phase order of the power supply to ensure correct operation.
Inspect External Chiller (If System is Water-Cooled):
- Confirm that the chiller refrigerant (IMTEK brand chillers use R-410A) is at the appropriate level.
- Verify that the chiller is receiving power; the display should indicate "OFF" when the CNP is not operational, as the CNP automates the chiller's activation.
- Check the water level in the chiller tank and ensure the cooling water flow rate is adequate.
- Inspect the circulation pump for possible failure.
- Check the water pressure gauge at the back of the chiller. If the pressure is "0 bar" (nominal value around 2 bar), check the water circulation pump and the water level in the chiller tank.
- Release any trapped air in the water line or pump if necessary.
- Ensure the ambient temperature is below 50°C for optimal chiller operation.
- Verify the chiller compressor is not seizing or choking regularly during operation. If issues persist, contact IMTEK Cryogenics.
Check for Leaks:
- Inspect the system for any signs of air or water leaks, or damage in the cooling or air intake lines.
Helium Compressor Check:
- Ensure the helium compressor is powered and not overheating. The inlet temperature should be below 21°C.
- Verify the static helium pressure, which should be at least 220 psig for all models.
Air Compressor Check:
- Listen for unusual noises which may indicate a problem with the motor or internal components.
- Inspect the capacitor for any signs of burning or damage. A faulty capacitor can prevent the compressor from starting or running properly.
- Ensure the cooling fan is working properly to prevent overheating. If the compressor is overheating, it may shut down or reduce efficiency.
- Check the air pressure gauge on the PLC screen to ensure the compressor is generating the correct pressure. If the pressure is low, there may be an issue with the compressor or a leak in the system. If the air compressor can not build enough pressure, call IMTEK Cryogenics.
If the cooling issue persists, contact IMTEK Cryogenics Service for in-depth support.
Frequently Asked Questions and Answers
Answer:
Regular maintenance should be performed every 8,000 hours (approximately two years) to ensure optimal performance. Refer to the user manual for specific maintenance schedules.